US Corrosion uses accelerated environmental testing as a crucial step in ensuring that materials and products can withstand the harsh and varied conditions they may encounter in real-world use.

The Fastest Possible Testing for Environmental Cracking
Environmental cracking includes a broad range of cracking mechanisms, including stress corrosion, hydrogen embrittlement, corrosion fatigue, and sour stress corrosion. Often the failures from these mechanisms can take months or years to occur, and most of the common testing techniques also take months or years for the testing. New technologies can not only perform these tests in only a few hours or days, but can also provide a quantitative evaluation of different materials, coatings, etc.

At US Corrosion, though, we utilize the rising step loads (RSL) testing methods to evaluate these same mechanisms in a matter of days or hours. For the first time, testing can be performed on a schedule that doesn’t interfere with production.
Accelerated Stress Corrosion Cracking Analysis
Accelerated stress corrosion cracking (SCC) analysis is a specialized method for evaluating the susceptibility of materials to stress corrosion cracking, which is a type of corrosion that results from the combined effects of mechanical stress and a corrosive environment. Accelerated SCC testing involves subjecting a material to a combination of mechanical stress and a corrosive environment in a laboratory setting, with the goal of inducing SCC in a shorter time frame than would occur under normal service conditions.
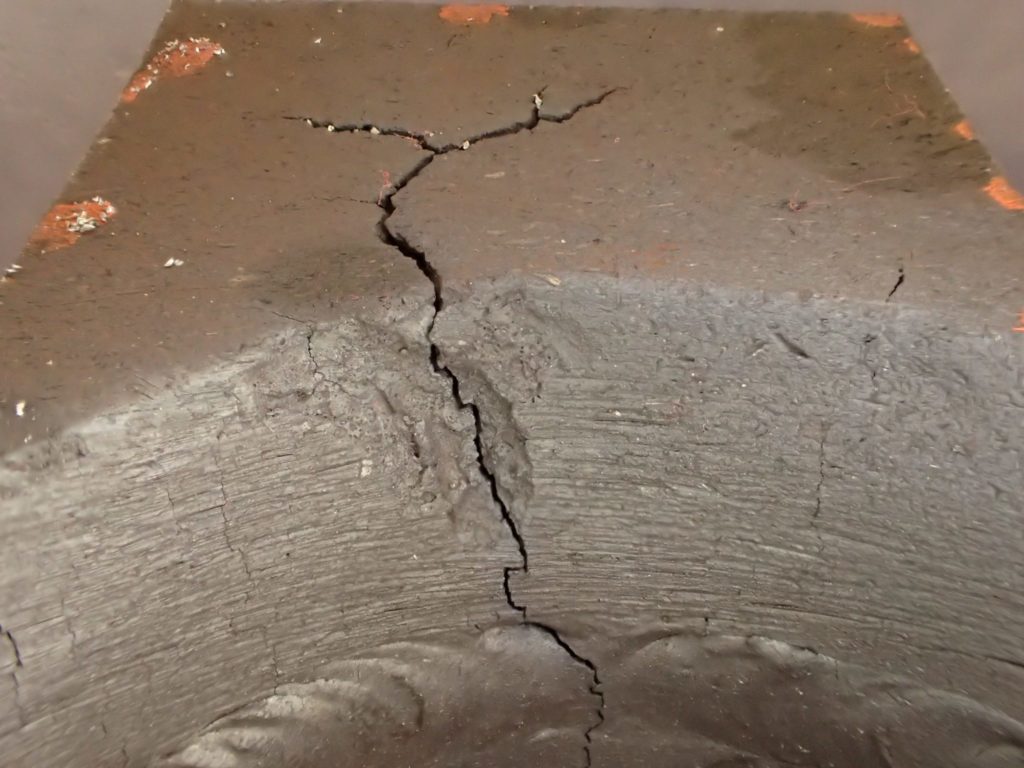
During an accelerated SCC test, the material is typically exposed to a constant load or cyclic loading, such as tension or bending, in the presence of a corrosive environment, such as a salt solution. The test may be performed at elevated temperatures to further accelerate the corrosion process. The material is periodically examined for signs of SCC, such as cracks or discoloration, and the test is typically run for a specified period of time, ranging from days to months.
Accelerated SCC analysis can provide valuable information on the susceptibility of materials to SCC, allowing manufacturers to evaluate the performance of materials under realistic service conditions and make informed decisions about material selection and design. US Corrosion is a leading provider of corrosion and metallurgical consulting services, and we have extensive expertise in accelerated SCC analysis. We can perform accelerated SCC testing on a wide range of materials and provide detailed analysis and recommendations based on the results. US Corrosion’s experts can also provide guidance on corrosion prevention and mitigation strategies to help manufacturers minimize the risk of SCC in our products.
Common sour corrosion testing like NACE TM0284 and TM0177 can take from a week to a month or more – and then you only get a pass/fail answer at a given stress level. Utilizing the patented RSL method, US Corrosion offers rapid sour corrosion cracking analysis that can be completed in as little as one day.
Rapid Hydrogen Embrittlement Analysis
In the example below, 3″ bolts were tested to evaluate hydrogen embrittlement susceptibility. The testing samples in the center are show as they will be tested, with the bolt threads being placed in tension by bending. This much more accurately replicate the actual load that the bolts would experience in service. Many specimens can be removed from a single bolt, allowing for testing at various cathodic protection levels or in different chemical solutions (cleaning chemicals, saltwater, etc.).
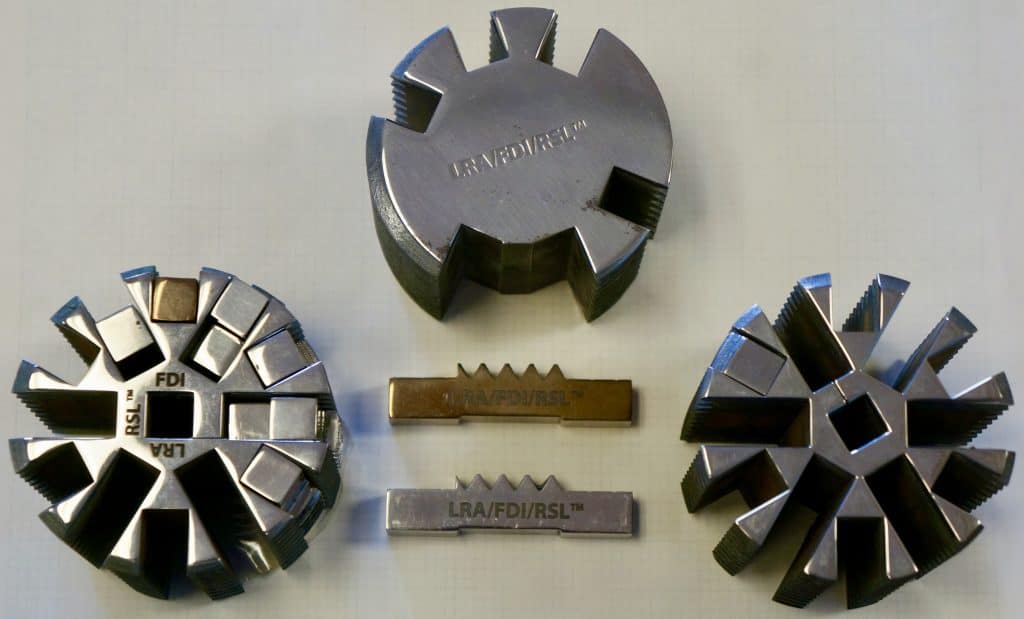
Rapid hydrogen embrittlement (HE) analysis is a specialized method for evaluating the susceptibility of materials to hydrogen embrittlement, which is a type of failure that can occur in materials exposed to hydrogen gas or hydrogen-containing environments. Rapid HE testing involves subjecting a material to a high concentration of hydrogen gas, typically in a laboratory setting, with the goal of inducing HE in a shorter time frame than would occur under normal service conditions.
During a rapid HE test, a material is typically exposed to a high-pressure hydrogen gas environment for a specified period of time, ranging from several hours to a few days. The material is then examined for signs of embrittlement, such as cracks or fractures, and the extent of the embrittlement is evaluated using specialized techniques such as fracture surface analysis.
Rapid HE analysis can provide valuable information on the susceptibility of materials to HE, allowing manufacturers to evaluate the performance of materials under realistic service conditions and make informed decisions about material selection and design. US Corrosion is a leading provider of corrosion and metallurgical consulting services, and we have extensive expertise in rapid HE analysis. We can perform rapid HE testing on a wide range of materials and provide detailed analysis and recommendations based on the results. US Corrosion’s experts can also provide guidance on corrosion prevention and mitigation strategies to help manufacturers minimize the risk of HE in our products.