Fracture toughness is a complex phenomena. Our experts can help you measure, understand, and use fracture toughness tests.
What is KIc fracture toughness?
KIc fracture toughness is a measure of a material’s resistance to crack propagation or fracture under tensile stress. It is a critical parameter in materials science and engineering, as it provides valuable information about the material’s ability to withstand and resist fracture, and is commonly used in the design and evaluation of structural components that are subjected to mechanical loading.
KIc fracture toughness is defined as the critical stress intensity factor required to initiate and propagate a crack in a material without catastrophic failure. It is a measure of the amount of energy required to propagate a pre-existing crack in a material, and is typically evaluated using standard test methods such as the ASTM E399 or the ISO 12135 test standards.

Image by Research Gate
How to Measure K1C Fracture Toughness Values
The KIc value is typically determined by measuring the load required to initiate a crack in a pre-cracked specimen, and then using this information to calculate the stress intensity factor at the crack tip. The KIc value is then calculated based on the critical stress intensity factor required to propagate the crack, which is typically measured using fracture mechanics testing methods.
The KIc fracture toughness value is influenced by a variety of factors, including the material’s microstructure, composition, processing, and testing conditions. As such, it is important to carefully control these factors during material selection and testing to ensure accurate and reliable KIc values are obtained.
Overall, the KIc fracture toughness is an important parameter that provides valuable information about a material’s ability to resist fracture and is commonly used in the development and testing of new materials and structural components. Learn more about the physics here from Iowa State.
How to measureKIc fracture toughness?
There are several methods for measuring KIc fracture toughness, but the most commonly used technique is the single-edge notched bend (SENB) test, which is standardized by ASTM E399 and ISO 12135. The SENB test involves measuring the load required to propagate a pre-existing crack in a notched specimen, and then using this information to determine the critical stress intensity factor required for crack propagation (KIc).
The SENB test is typically performed using a universal testing machine equipped with a three-point bending fixture that supports the specimen and applies a controlled load. The specimen is typically machined from a larger sample and has a notch or crack machined into it to create a pre-existing crack. The size and shape of the notch are carefully controlled to ensure that the crack propagates in a stable and controlled manner.
Calculating the Critical Stress Intensity Factor
During testing, the specimen is loaded at a constant rate until the crack propagates, and the load and crack length are continuously recorded. The critical stress intensity factor is then calculated using the following equation:
KIc = (Pmax / B) x (W / 2 + a)^(1/2) / Y
Where Pmax is the maximum load, B is the specimen thickness, W is the specimen width, a is the crack length, and Y is a dimensionless correction factor that depends on the specimen geometry and loading conditions.
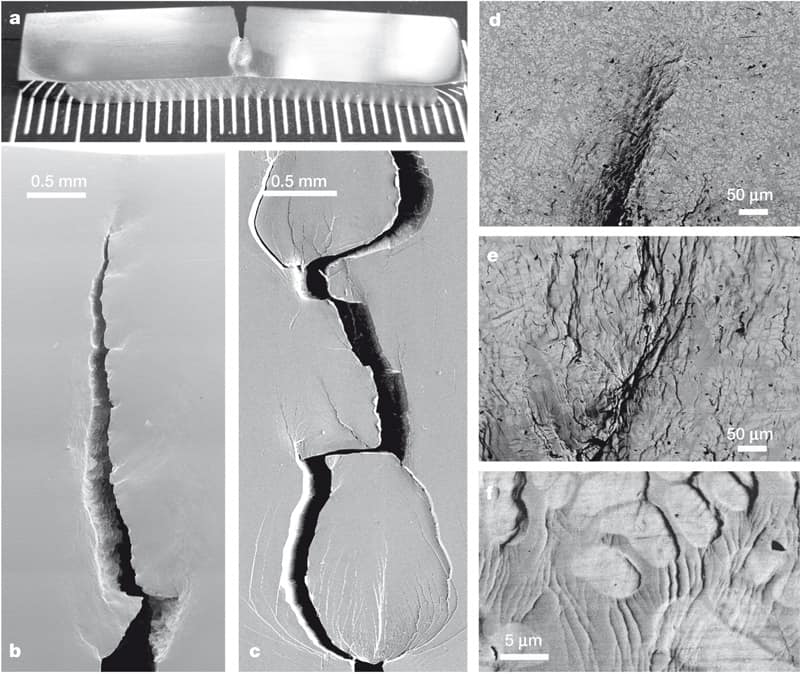
Image by Research Gate
Testing Methods to Measure Fracture Toughness
The KIc value obtained from the SEN(B) test is influenced by several factors, including the specimen geometry, loading conditions, and material properties such as yield strength and fracture toughness. As such, it is important to carefully control these factors during testing and to follow standardized test procedures to ensure accurate and reliable results.
In addition to the SEN(B) test, other techniques for measuring KIc fracture toughness include the compact tension (CT) test, the chevron notched beam (CNB) test, and the double-edge notched tension (DENT) test. Each of these tests has its own advantages and disadvantages, and the choice of test method depends on the specific application and material properties of interest.
In our lab we use the RSL method, which is a much faster test of K1C that is designed for accurate determination of fracture toughness. US Corrosion provides rapid K1C fracture toughness testing, with turnaround as quick as next-day service available. We test per ASTM E399 and other related methods. An example of environmental K1C fracture toughness testing is shown below with an applied voltage on the sample, which is loaded in bending:
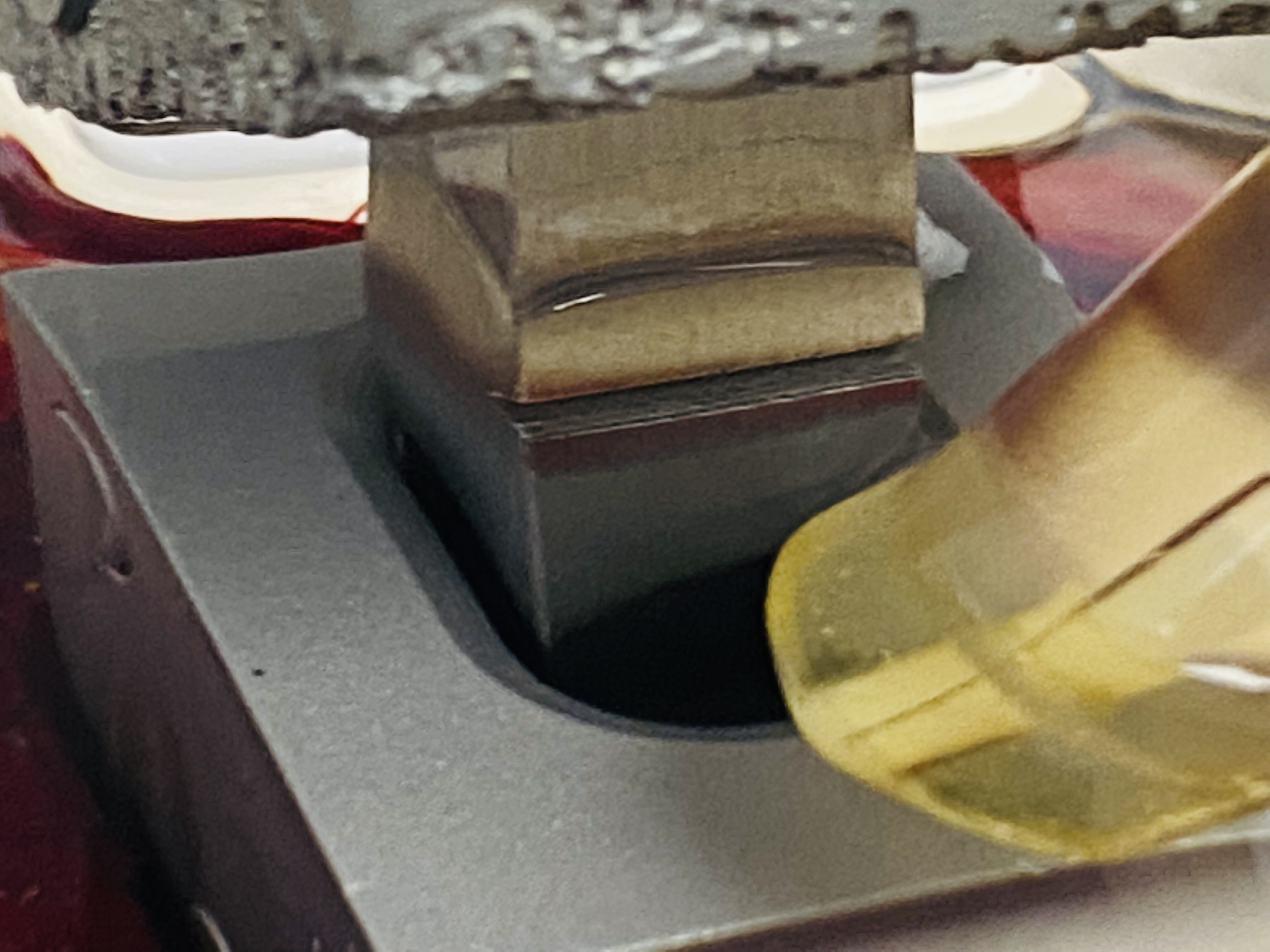
When do I need K1C fracture toughness testing?
There are several situations where knowledge of the KIc fracture toughness is essential. For example, in the aerospace industry, KIc fracture toughness is critical for the design and evaluation of aircraft structures and components, such as wings, fuselages, and landing gear. These components are subjected to high mechanical stresses and must be able to resist fatigue and fracture over their service life. Knowledge of the KIc value is therefore essential for ensuring the safety and reliability of aircraft structures.
Similarly, in the automotive industry, KIc fracture toughness is important for the design and evaluation of engine components, such as crankshafts, camshafts, and gears. These components are subjected to high mechanical stresses and must be able to withstand fatigue and fracture during operation. Knowledge of the KIc value is therefore essential for ensuring the durability and reliability of automotive components.
Many different mechanism affect the fracture toughness, including secondary phases, fine grain structure, grain boundaries, micro cracking, and more. Our experts can help you evaluate these different mechanisms and properties of the material, to determine what is influencing your materials.

K1C vs. Charpy impact testing?
K1C fracture toughness testing and Charpy impact testing are both methods used to evaluate the mechanical properties of materials, but they are used for different purposes and measure different parameters.
K1C fracture toughness testing is used to measure the critical stress intensity factor required to initiate and propagate a crack in a material without catastrophic failure. It is typically performed using a single-edge notched bend (SENB) test as described earlier. The K1C value obtained from this test provides valuable information about the material’s ability to resist fracture and crack propagation under tensile stress.
Charpy impact testing, on the other hand, is a type of dynamic testing used to measure a material’s resistance to impact or shock loading. It involves striking a notched specimen with a pendulum and measuring the amount of energy absorbed by the specimen during fracture. The Charpy impact test provides valuable information about a material’s toughness, which is its ability to absorb energy and deform plastically before fracturing.
While both K1C fracture toughness testing and Charpy impact testing provide valuable information about a material’s mechanical properties, they measure different parameters and are used for different purposes. K1C fracture toughness testing is typically used to evaluate a material’s resistance to crack propagation under tensile stress, while Charpy impact testing is typically used to evaluate a material’s toughness and resistance to impact or shock loading. If you aren’t sure what is best for you, contact us and our engineers can help you select the right analyses!