Measure, Understand, and Prevent Hydrogen Embrittlement
Hydrogen is a paradox – it’s the smallest element but can bring down the largest structure. Almost all high-strength materials are subject to failure by hydrogen embrittlement (HE) at sufficient levels. Our experts help determine the cause and prevent hydrogen-related failures.
However, the economic value of using high-strength materials makes them a preferable choice in many applications. Unfortunately, improper fabrication or thermal exposure can damage high-strength materials. Excessive temperature exposure can produce hydrogen-cracking susceptible materials.
The most common method for checking strength of materials (tensile testing) will not reveal this problem, leaving a possibly fatal blindspot. With our extensive experience in hydrogen embrittlement analysis and consulting issues, US Corrosion is uniquely well suited to help with a wide range of HE projects. Common services we offer include:
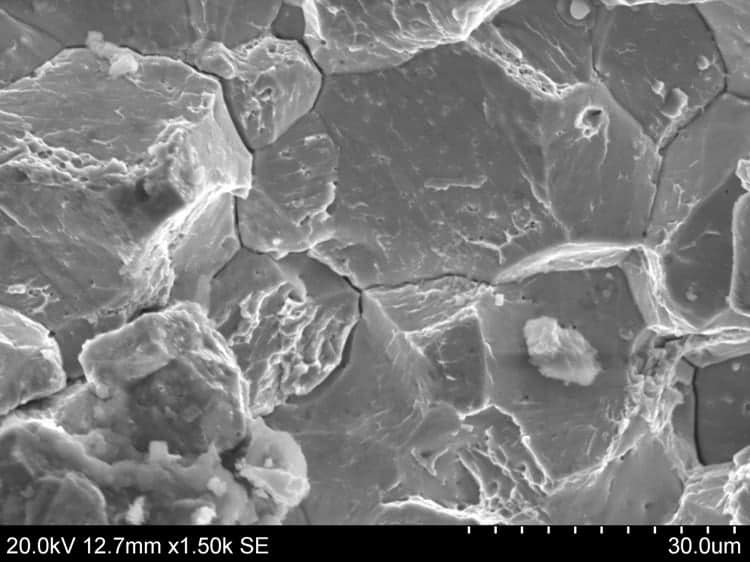
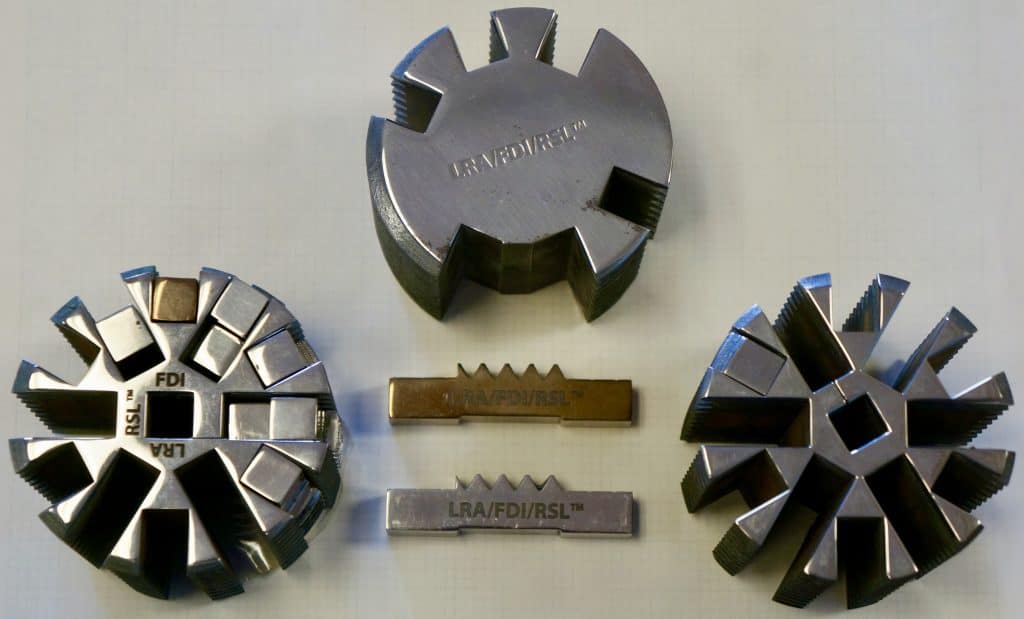
- HE Consulting by PhD Experts
- Hydrogen-Related Failure Analysis
- R&D for Hydrogen Embrittlement
- Equipment for Routine QA HE Testing
Consulting for Hydrogen Embrittlement – From R&D to Failure Analysis
Our experts bring decades of experience to bear on HE and other environmentally-assisted cracking (EAC) mechanisms, helping you understand the problem and prevent it from occurring. We employ a variety of analytical testing for hydrogen embrittlement and EAC to confirm the effects of hydrogen, which can be used for:
Batch-per-batch Analysis of Materials for Hydrogen Embrittlement
When materials are susceptible to hydrogen embrittlement, it’s important to test every batch to ensure that it’s safe for use. In fact, ASTM F519, B577, F1624, and F1940 and other standards are specifically designed for this purpose. US Corrosion is a leader in providing these rapid hydrogen embrittlement analyses.
What Causes Hydrogen Embrittlement?
Hydrogen embrittlement is a type of failure that occurs in metals and alloys when they are exposed to hydrogen gas or hydrogen-containing environments. The exact mechanisms of hydrogen embrittlement are complex and not fully understood, but there are a few factors that are known to contribute to this phenomenon.
One of the main causes of hydrogen embrittlement is hydrogen absorption. Hydrogen is a very small atom that can easily diffuse into metals and alloys, where it can accumulate and interact with the microstructure of the material. When hydrogen interacts with the material’s microstructure, it can cause changes in the material’s mechanical properties, such as reduced ductility and increased hardness. This can lead to cracking, fracture, and ultimately, failure of the component.
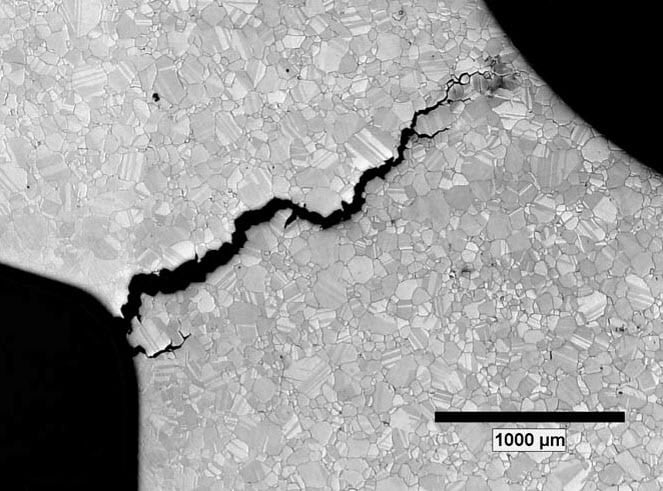
Image by Research Gate
Another cause of hydrogen embrittlement is residual stress. Residual stress can result from a variety of factors, including manufacturing processes, welding, and surface treatments. When a material is exposed to hydrogen gas or a hydrogen-containing environment, the residual stress can interact with the hydrogen and cause changes in the material’s mechanical properties, leading to cracking and failure.
Finally, hydrogen embrittlement can be caused by environmental factors, such as exposure to high-pressure hydrogen gas or exposure to hydrogen-containing chemicals. In these cases, the hydrogen can rapidly diffuse into the material and cause embrittlement, even in materials that are typically resistant to hydrogen embrittlement.
Preventing hydrogen embrittlement requires a comprehensive approach that includes material selection, design optimization, and preventative measures. US Corrosion is a leading provider of corrosion and metallurgical consulting services, and they have extensive expertise in understanding and preventing hydrogen embrittlement. They can provide guidance on material selection and design optimization, as well as perform testing and analysis to evaluate the susceptibility of materials to hydrogen embrittlement and identify potential failure points.
Hydrogen Embrittlement Research and Development
We employ the RSL (aka Incrememental step load) method for performing a wide range of hydrogen embrittlement research and development (R&D) activities. From the Bay Bridge to household screws, we’ve evaluated an enormous variety of materials, chemicals, cleaners, and environments for customers of all kinds. The RSL technology is uniquely powerful for R&D of hydrogen because it enables testing in all kinds of simulated conditions, loads, temperatures, environments, and more. Our experienced corrosion experts can help you produce an optimized analysis process for R&D using design of experiments and statistics to ensure you can effectively and rapidly evaluate many different variables.
Hydrogen Embrittlement Failure analysis
RSL is also critical to our hydrogen embrittlement failure analysis activities. In many cases, the failed specimens are quite small; with RSL testing, we can accommodate samples as small as 1″ in length. This means we can accurately assess the hydrogen-induced cracking susceptibility of even very small failed components.
In other cases, such as the Bay Bridge bolts, the standard RSL samples provided equivalent data to expensive large-scale tests. RSL analyses have been proven many times to provide equivalent results to large-scale tests. Since they can be performed for a fraction of the cost and time, RSL is a preferred method for evaluating hydrogen-related failures. We combine the RSL analysis with our traditional metallurgical failure analysis and corrosion analysis capabilities to help you have certainty in the diagnoses of your failure mechanisms.
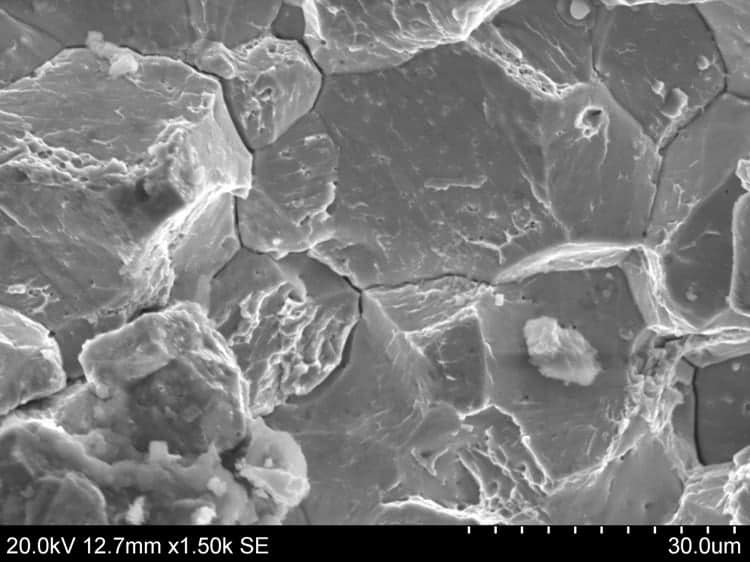
ASTM Hydrogen Embrittlement Testing Services
We offer hydrogen embrittlement testing in accordance with ASTM F519, ASTM F1624, ASTM F1940, and many other similar methods. Our experts participate in the committees and keep up with the latest changes, and we can help you ensure you are in compliance with the relevant ASTM, ISO, or other standards. Here’s a list of many of the ASTM hydrogen embrittlement tests we provide:
- ASTM A1032 – Testing for HE Resistance of Cold Drawn Steel Wire in Prestressed Concrete Pipe – This is for hard-drawn steel wire, and testing is performed in an ammonium thiocyanate environment,
- ASTM B577 – (Similar to ISO 2626) – Detection of Cuprous Oxide (Hydrogen Embrittlement Susceptibility) in Copper – This test is to ensure that copper products are truly oxygen-free. It can be performed by several methods ranging from simple metallography to high-temperature exposure to gaseous hydrogen,
- ASTM B839 – “The Wedge Test” – Testing for Embrittlement in Metallic Coated, Externally Threaded Articles like Fasteners using the Rod-Inclined Wedge Method – typically used for threaded components, fasteners, and rod materials,
- ASTM B849 – For Pre-Treatments of Iron or Steel for Reducing Risk of Hydrogen Embrittlement – OK, technically don’t actual offer this test, because its a method for specifying heat treatments to prevent hydrogen embrittlement. Instead, we offer consulting and testing to help select the right heat treatments and to ensure they worked!
- ASTM B850 (aka ISO 9588) – Guide for Post-Coating Treatments of Steel for Reducing the Risk of Hydrogen Embrittlement – Again, we don’t do this test since it’s not a test – but we provide guidance on how to select the proper post-coating heat treatments and be sure they worked!
- ASTM F1459 – For Determination of the Susceptibility to Hydrogen Embrittlement by Gaseous Hydrogen – This is challenging and complicated test that uses diaphragms loaded at different pressures to determine the effect on burst pressures,
- ASTM F519 – Method for Mechanical Hydrogen Embrittlement Evaluation of Plating/Coating Processes and Service Environments – We provide both the rising step load (better and faster) and sustained load (cheap but slow and old school) versions of this test, and
- ASTM G142 – Determination of Susceptibility of Metals to Embrittlement in Hydrogen Containing Environments at High Pressure, High Temperature, or Both – This test is for HPHT conditions such may occur in refineries, drilling, aerospace, and many other applications.