ASTM F519 Hydrogen Embrittlement Testing Services and Equipment
Platings and coatings can lead to hydrogen embrittlement of high-strength steels. A widely used method for preventing hydrogen embrittlement is ASTM F 519 hydrogen embrittlement test. The method uses either sustained loads or rising step loads (our preferred method) for routine testing of plating/coating operations.
US Corrosion Services is the leading provider of hydrogen embrittlement (HE) testing services and equipment, ideal for ASTM F519, F1624, F1940, and other forms of environmental cracking . We can help you rapidly determine if materials are subject to HE using the rising step load (RSL) testing method, or more slowly using the pass/fail sustained load test version. We perform ASTM F 519 testing for many industries, including aerospace, energy, automotive, and transportation customers.
To complement our F519 hydrogen embrittlement testing, we also offer expert consulting on hydrogen-related failures – including when you have a batch that does not pass F519. We use tools like the electron microscopy shown below to evaluate the fracture surfaces and confirm that HE is the cause of failure and not some other issue. The intergranular fracture seen in the picture below is a classic indicator of hydrogen embrittlement. However, non-HE failures during F519 can occur due to defects, bad machining, mis-aligned machines, and other reasons. We apply decades of experience to help you understand and prevent failures, including help with coating and plating bath optimization.
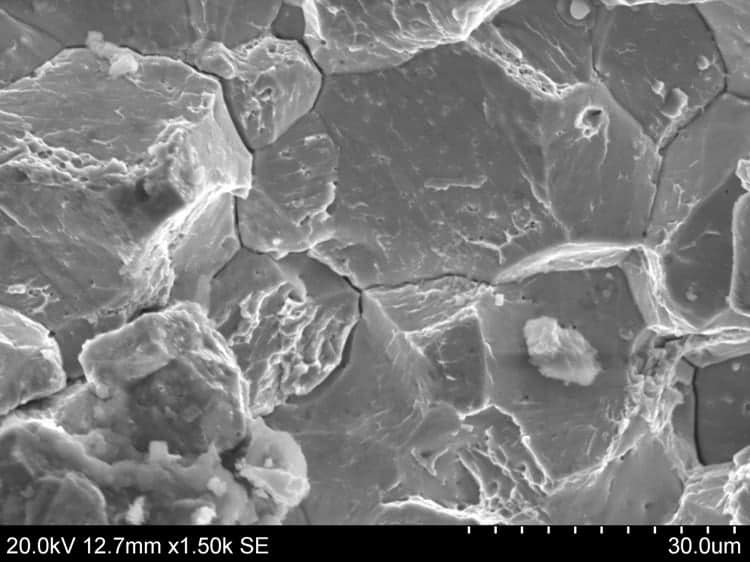
Our consulting also includes help with issues when you have a batch that does not pass F519. We use tools like the electron microscopy shown below to evaluate the fracture surfaces and confirm that HE is the cause of failure and not some other issue. The intergranular fracture seen in the picture below is a classic indicator of hydrogen embrittlement. However, non-HE failures during F519 can occur due to defects, bad machining, mis-aligned machines, and other reasons. We apply decades of experience to help you understand and prevent failures, including coating and plating bath optimization.
we also offer expert consulting on hydrogen-related failures – including when you have a batch that does not pass F519. We use tools like the electron microscopy shown below to evaluate the fracture surfaces and confirm that HE is the cause of failure and not some other issue. The intergranular fracture seen in the picture below is a classic indicator of hydrogen embrittlement. However, non-HE failures during F519 can occur due to defects, bad machining, mis-aligned machines, and other reasons. We apply decades of experience to help you understand and prevent failures, including coating and plating bath optimization.
What is Hydrogen Embrittlement Testing?
Hydrogen embrittlement testing is crucial for finding dangerous materials before they go into service. High-strength materials like steels and aluminum can fail prematurely if they haven’t been produced correctly – but unfortunately, this cannot be confirmed visually or by a tensile test. Therefore, HE testing is used on many materials to help find and prevent dangerous materials from going into service.
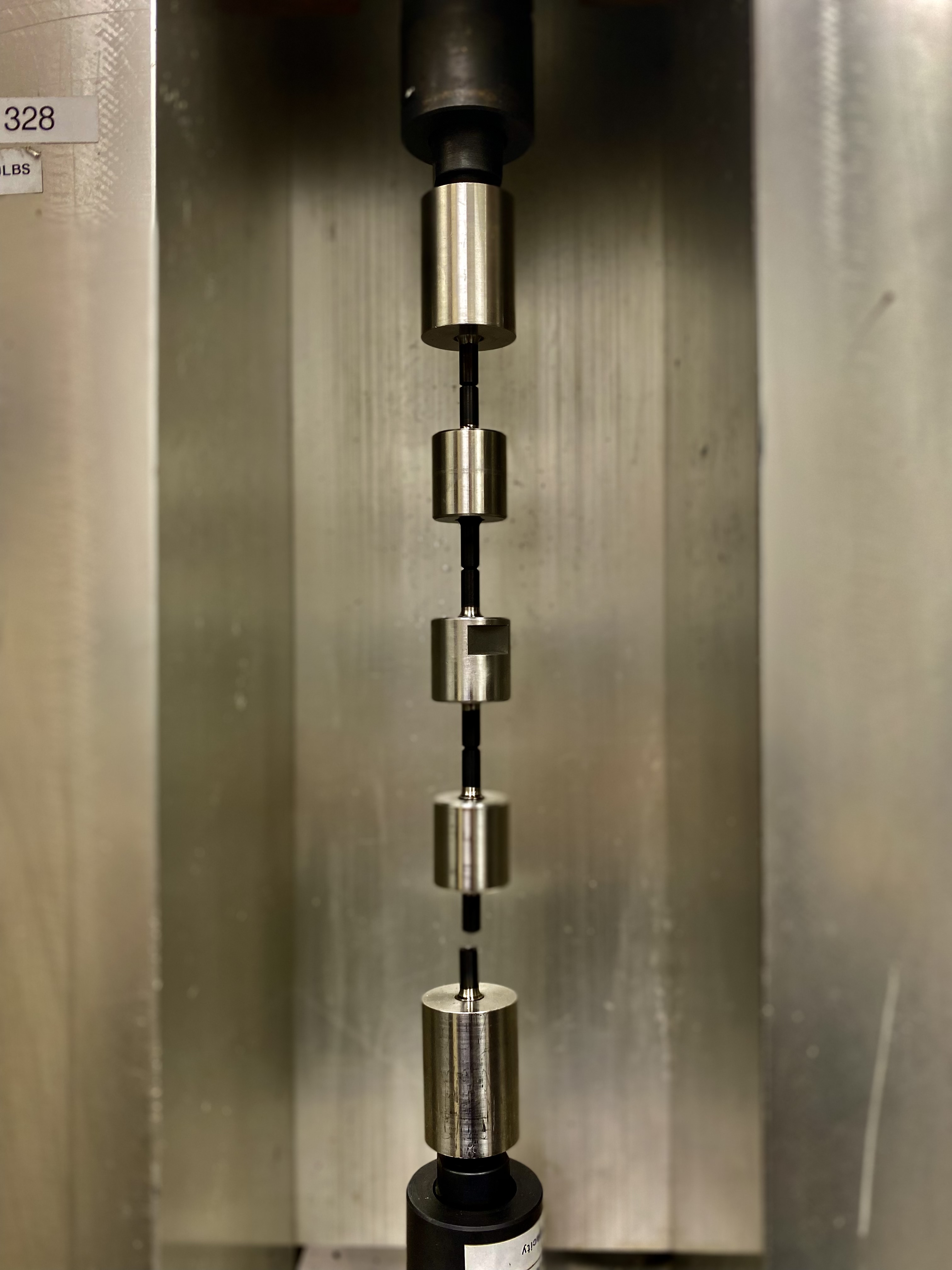
Ultimately, hydrogen embrittlement occurs when hydrogen is generated during plating processes (often called internal HE) or during service conditions (external HE). When too much hydrogen is present in high-strength parts, they can become brittle. Routine testing is required for many coated, plated, or high-strength components to ensure they are not susceptible to hydrogen embrittlement.
We can test with various liquids, including saltwater or cleaning chemicals, and using applied cathodic protection at varying levels. US Corrosion is partnered with Dr. Lou Raymond, the developer of the RSL testing methodology, with over 40 years of experience in HE testing. We also provide hydrogen embrittlement consulting and failure analysis services.
What Types of Hydrogen Embrittlement Tests are Common?
US Corrosion offers three common versions of F 519: 200-hour sustained load testing (SLT), 200-hour SLT plus rising step load (RSL), and RSL alone. RSL testing is by far the fastest – it can usually be completed in just 1-2 days. In comparison, the SLT version takes 8 days minimum.

ASTM F519 is very specifically designed for testing plating operations, while F1624 is much more broadly applicable. Fortunately, our experts also have extensive experience in using ASTM F1624 testing for characterization, research, and failure analysis, as well as testing fluids and chemicals for their potential to cause HE.
What Testing Equipment is Right for Hydrogen Embrittlement?
There are two common ways to test for hydrogen embrittlement from plating, coating, or of alloys. There are also several related methods for testing other forms of environmental cracking. In addition to testing services, we provide cutting-edge equipment for ASTM F519 testing using both tensile and bending frames. To learn more about our RSL testing frames and how you can quickly perform RSL testing in-house, let’s talk! The RSL testing systems that we use and offer for sale are load-displacement controlled with software developed over decades to be able to evaluate hydrogen embrittlement in a wide variety of circumstances.
If you are testing routinely for a plating bath or similar operations, we suggest our baseline system for running ASTM F519. A single system can provide testing for 3-4 lines on a weekly basis, or multiple machines can be used to test every day. Testing more often can save you in the long-run by preventing much more costly scrapping and recalls of parts.
On the other hand, if you want to test samples from actual parts or after service, we recommended our advanced system, which can run more complex tests in accordance with ASTM F1624 (and will also do F519). If you aren’t sure, contact our experts for advice!
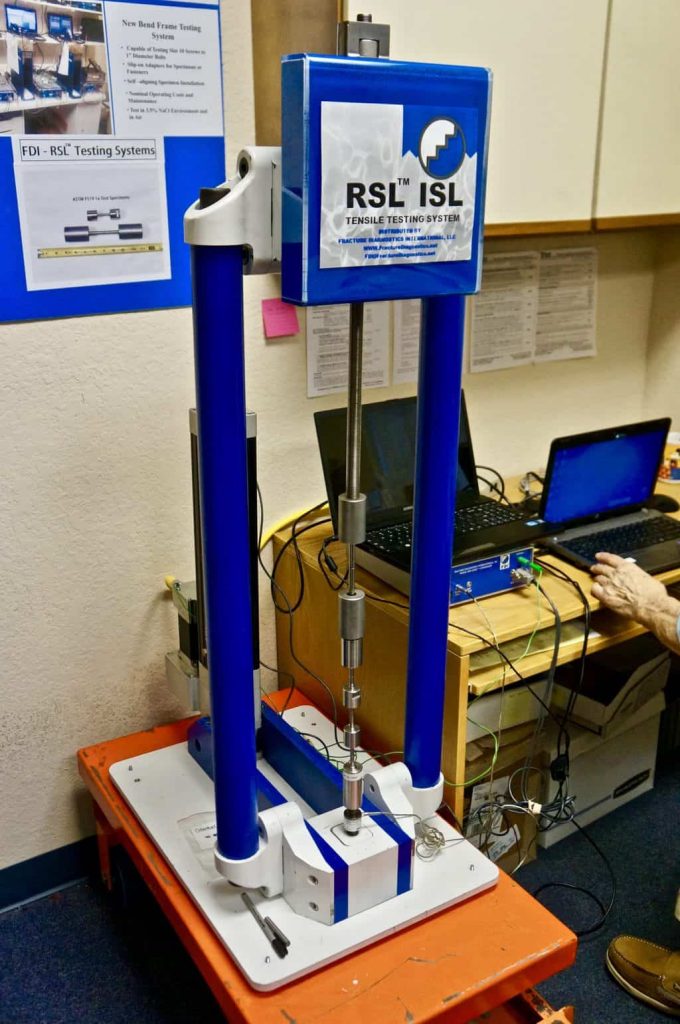
Hydrogen Embrittlement Consulting Services and Expert Witness Services
We support customers to deal with (1)
Our experts are highly active in the ASTM committees making the most common standards, like F519, F1624, and F1940.