Welder qualification is a critical process that ensures the quality and safety of welded structures and equipment. This process involves testing and inspecting welders to ensure that they have the knowledge, skill, and experience to perform specific welding tasks. At our webpage, we provide valuable information and insights on welder qualification, including industry standards and regulations, testing and inspection methods, qualification criteria, and the benefits of welder qualification. Whether you are a welder, welding professional, or organization involved in welding operations, our webpage can help you understand the importance of welder qualification and provide guidance on how to become a qualified and certified welder.
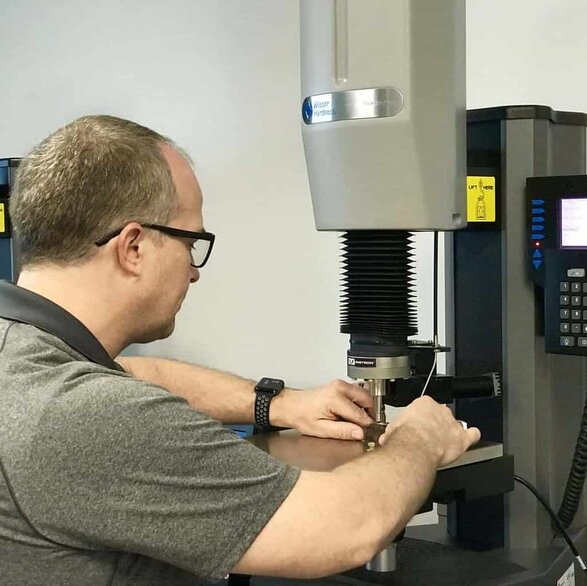
One of US Corrosion’s welding experts!
Qualification criteria
Qualification criteria are a set of requirements that welders must meet to demonstrate their ability to perform specific welding tasks. At US Corrosion, we understand the importance of qualification criteria in ensuring the quality and safety of welded structures and equipment. Our team of experts has extensive experience in developing and implementing qualification criteria for various welding processes and positions.
The qualification criteria for welders typically include the following:
- Materials being welded: The type of materials being welded can affect the welding process and the quality of the weld. Welders must be qualified to work with specific materials, including different grades of steel, aluminum, and other metals.
- Thickness of the materials: The thickness of the materials being welded can affect the welding process and the quality of the weld. Welders must be qualified to work with specific thicknesses of materials, as specified by industry standards and regulations.
- Welding positions: Welders must be qualified to perform specific welding positions, including flat, horizontal, vertical, and overhead positions. Each position requires different welding techniques and presents unique challenges that welders must be able to overcome.
- Welding processes: Welders must be qualified to perform specific welding processes, including stick welding, MIG welding, TIG welding, and others. Each process has its own set of requirements and presents different challenges that welders must be able to overcome.
- Welding codes and standards: Welders must be familiar with industry codes and standards, including those set by the American Welding Society (AWS) and the Occupational Safety and Health Administration (OSHA). Welders must be able to apply these codes and standards to their work to ensure compliance and safety.
At US Corrosion, we work closely with our clients to develop and implement qualification criteria that meet their specific needs and comply with industry standards and regulations. Our team of experts can help clients identify the specific qualification criteria required for their welding projects and provide guidance and support throughout the qualification process. By ensuring that welders meet the necessary qualification criteria, we can help our clients achieve high-quality welds that meet industry standards and ensure the safety and reliability of their structures and equipment.
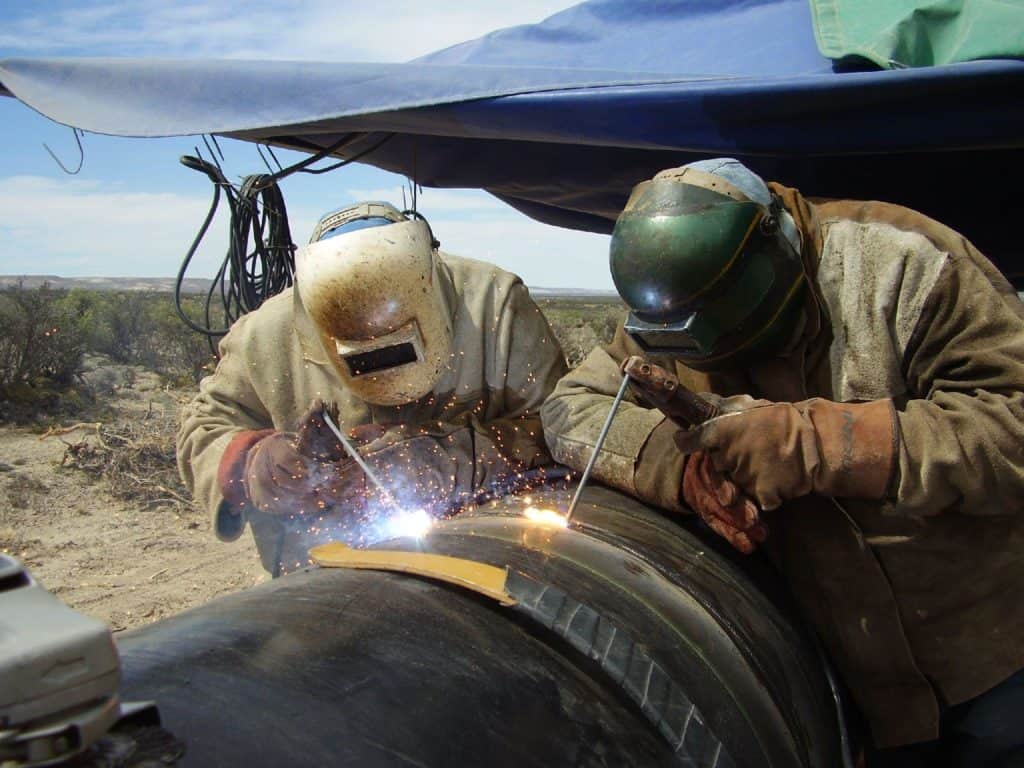
image by Canadian Metal Working
Welder Certification
Welder qualification and certification are two distinct but related processes in the welding industry. Welder qualification is the process of testing and inspecting welders to ensure that they have the necessary skills, knowledge, and experience to perform specific welding tasks. This process involves evaluating the welder’s ability to work with specific materials, thicknesses, welding positions, and welding processes.
Welder certification, on the other hand, is a process that verifies that a welder has met specific industry standards and regulations for a particular welding process and position. Certification is typically required by industry standards and regulations, and it is often a prerequisite for employment in certain welding-related jobs.
To become certified for specific welding processes and positions, welders must first undergo a qualification process. This process involves testing and inspecting the welder’s ability to perform specific welding tasks, as well as verifying that the welding procedure used meets industry standards and regulations. Once the welder has been qualified, they can then become certified by passing a certification exam.
Welder certification exams typically include a written portion and a practical portion. The written portion tests the welder’s knowledge of welding theory, safety, and industry standards and regulations. The practical portion involves performing a weld to demonstrate the welder’s ability to work with specific materials, thicknesses, welding positions, and welding processes.
At US Corrosion, we provide comprehensive welding services, including welder qualification and certification. Our team of experts can help welders navigate the qualification and certification process, providing guidance and support to ensure that they meet industry standards and regulations. We can also help businesses and organizations ensure that their welders are qualified and certified to perform specific welding tasks, thereby ensuring the safety and reliability of their structures and equipment.
Welding Processes and Positions
Welders can be qualified for different welding processes and positions depending on the specific requirements of the project or industry standards and regulations. At US Corrosion, we have extensive experience in qualifying welders for various welding processes and positions, including:
Welding Processes:
- Stick welding (SMAW)
- Gas tungsten arc welding (GTAW or TIG)
- Gas metal arc welding (GMAW or MIG)
- Flux-cored arc welding (FCAW)
- Submerged arc welding (SAW)
- Plasma arc welding (PAW)
- Laser beam welding (LBW)
- Electron beam welding (EBW)
- Resistance welding
Welding Positions:
- Flat position
- Horizontal position
- Vertical position
- Overhead position
- 1G position (rotated flat)
- 2G position (rotated horizontal)
- 3G position (rotated vertical)
- 4G position (overhead rotated)
Each welding process and position requires different techniques and presents unique challenges that welders must be able to overcome. By qualifying welders for specific welding processes and positions, employers can ensure that their welders have the necessary skills and knowledge to perform welding tasks safely and efficiently.
At US Corrosion, we work closely with our clients to identify the specific welding processes and positions required for their projects or operations. We can then develop and implement qualification criteria and provide guidance and support to help welders become qualified for those specific processes and positions. Our goal is to ensure that our clients have a qualified and skilled workforce that can meet the demands of their welding operations and comply with industry standards and regulations.